-
Alumina Ceramic Components
-
Ceramic Housing
-
Metallized Alumina Ceramics
-
Custom Ceramic Parts
-
Alumina Ceramic Insulator
-
Alumina Ceramic Rings
-
Pressure Sensor Ceramic
-
Advanced Technical Ceramics
-
Advanced Engineering Ceramics
-
Fuse Ceramic
-
Ceramic Connector Blocks
-
Electronic Ceramic Components
-
Magnetron Ceramic
-
Zirconia Ceramic Parts
-
Alumina Ceramic Rods
-
Mr.FarnReply very fast and easy to talk!
-
Mr.JacksonGood service and nice to talk.
High Stability Microwave Magnetron Ceramic IATF16949 Industrial Ceramics
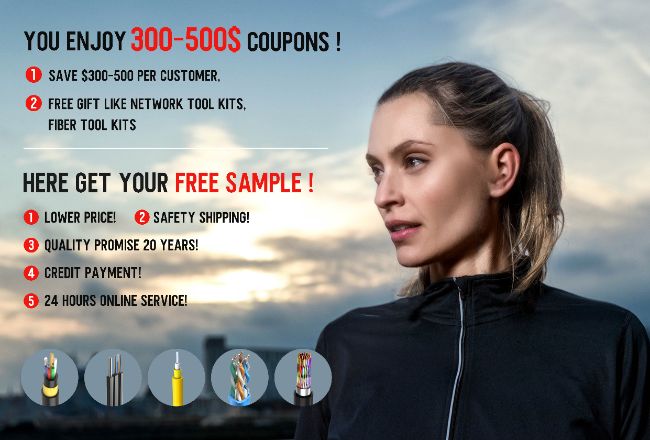
Contact me for free samples and coupons.
Whatsapp:0086 18588475571
Wechat: 0086 18588475571
Skype: sales10@aixton.com
If you have any concern, we provide 24-hour online help.
xProduct Name | Microwave Magnetron Ceramic | Material | Alumina (Aluminum Oxide, Al2O3) |
---|---|---|---|
Density | 3.7g/cm3-5.9g/cm3 | Power Range | ≤7W /cm2 |
Working Temperature | -40℃-125℃ | Pressure | ≦ 10-3Pa |
Working Voltage | 3v~480v | Thermal Shock Test | 1.(Temperature):-55℃/125℃ 2,(Time)2.2min 3 (Switching Time ) Max 10s 4 (Frequency):15 Times |
Working Life | >5000 H | ||
Highlight | High stability Magnetron Ceramic,IATF16949 Magnetron Ceramic,IATF16949 industrial ceramics |
Home Electrical Microwave Magnetron Ceramic / Special Ceramic Parts
1. Description:
Alumina is the most well-known and most commonly used fine ceramic material. It has the same sintered crystal body as sapphire and ruby. It has been used for decades in electrical components for its high electrical insulation, and is widely used in mechanical parts for its high strength, and corrosion- and wear-resistance.It is the most well-known fine ceramic material for chemical and physical stability.Its producing process as below:
Powder Preparation Understanding how raw powder contributes to the final properties of fired ceramics is key to providing components that meet the challenges of your application.
Forming There are several basic forming methods such as Isostatic Pressing, Extrusion, Injection Molding, Mechanical Pressing.
Green Machining The machining of a ceramic in the unfired state is called green machining. Green machining of ceramics is done whenever possible since the machining of ceramics after firing is very costly.
Firing In order for ceramic to be hard and dense, they must be "sintered", or fired to high temperatures for prolonged periods of time in gas or electric kilns.
Coating / Glazing One of the reasons that parts are glazed is to make it easy to remove unwanted residue. For instance, spark plugs are glazed to reduce areas of potential arcing in high voltage environments.
Grinding & Cleaning Grinding and cleaning are part of the after firing operations, please find detailed descriptions for each process at the link above.
Metalizing & Plating We produce thick film metalization inks that utilize a Moly-Manganese (MoMn) refractory formulation designed for oxide ceramic bodies to provide one of the industry's strongest bond strengths.
2. Feature Advantages:
1) High elasticity modulus
2) High compressive strength.
3) Anti corrosion
4) Abrasion resistance
5) Impact resistance
6) High precision
7) High stability
8) Good advanced ceramic materials
9) High welding sealing performance
10) High hardness and high density
11) Low thermal conductivity
12) Chemical inertness
13) Good wear resistance
14) High Fracture toughness
15) Good insulation performance
16) High temperature resistance
3. Material Features / Properties:
Color | White or Ivory | White or Ivory | White or Ivory | |
Density | g/cm 3 | 3.82 | 3.9 | 3.92 |
Hardness | HRA | 83 | 85 | 85 |
Flexural Strength | Mpa (psi*10 3 ) | 375 | 386 | 381 |
4. Technical Parameters:
Technical Parameters of Ceramics | ||||||||
Items | Test Conditions | Unit or Symbol | 99% AL2O3 | 95% AL2O3 | 90% AL2O3 | Zirconia | Steatite | Silicon Carbide |
Volume Density | -- | g/cm3 | ≥3.70 | ≥3.62 | ≥3.40 | ≥5.90 | ≥2.60 | ≥3.08 |
Tightness | -- | Pa·m³/s | ≤1.0×10-11 | ≤1.0×10-11 | ≤1.0×10-11 | - | - | - |
Liquid Permeability | -- | -- | Pass | Pass | Pass | Pass | - | |
Flexural Strength | - | MPa | ≥300 | ≥280 | ≥230 | ≥1100 | ≥120 | ≥400 |
Elastic Modulus | - | GPa | - | ≥280 | ≥250 | ≥220 | - | 400 |
Poisson Ratio | - | - | - | 0.20~0.25 | 0.20~0.25 | - | - | - |
Thermal Shock Resistance | 800℃( Room Temperature) Cycle: 10 times | Pass | Pass | Pass | - | - | - | |
Coefficient of Linear Expansion | 20℃~100℃ | ×10-6 K-1 | - | - | - | ≤8 | - | |
20℃~500℃ | ×10-6 K-1 | 6.5~7.5 | 6.5~7.5 | 6.5~7.5 | 6.5~11.2 | - | - | |
20℃~800℃ | ×10-6 K-1 | 6.5~8.0 | 6.5~8.0 | 6.3~7.3 | - | 4 | ||
20℃~1200℃ | ×10-6 K-1 | - | 7.0~8.5 | - | - | - | - | |
Coefficient of Thermal Conductivity | 20℃ | W/(m·k) | - | - | - | - | - | 90~110 |
1000℃ | ||||||||
Dielectric Constant | 1MHz 20℃ | - | 9.0~10.5 | 9.0~10 | 9.0~10 | - | ≤7.5 | - |
1MHz 50℃ | - | - | 9.0~10 | - | - | - | - | |
10GHz 20℃ | - | 9.0~10.5 | 9.0~10 | 9.0~10 | - | - | - | |
Volume Resistivity | 100℃ | Ω·cm | ≥1.0×1013 | ≥1.0×1013 | ≥1.0×1013 | - | ≥1.0×1012 | - |
300℃ | ≥1.0×1013 | ≥1.0×1010 | ≥1.0×1013 | - | - | - | ||
500℃ | ≥1.0×109 | ≥1.0×108 | -- | - | - | - | ||
Disruptive Strength | D.C | kV/mm | ≥17 | ≥15 | ≥15 | - | ≥20 | - |
Chemical Durability | 1:9HCl | mg/c㎡ | ≤0.7 | ≤7.0 | - | - | - | - |
10%NaOH | mg/c㎡ | ≤0.1 | ≤0.2 | - | -- | - | - | |
Grain Size | - | μm | - | 3~12 | - | - | - | - |
5. Process Flows:
Formulating --- Granulating --- Forming --- Sintering --- Grinding --- Printing --- Nickel Plating --- Inspecting --- Packing
6. Application Fields:
Microwave Magnetron Ceramic for Home Electrical Appliances , Aerospace and Other Industry!
7. Production Facilities: Prilling Tower , Forming Machine , High Temperature Sintering Kiln
8. Detection Devices:
Electric Performance Tester , Film Thickness Analyzer , Granulometer , Helium Mass Spectrometer Leak Detector , Universal Pull Force Meter
9. Notes:Above information only for reference and please contact with us for more details freely when you have any inquiry!