-
Alumina Ceramic Components
-
Ceramic Housing
-
Metallized Alumina Ceramics
-
Custom Ceramic Parts
-
Alumina Ceramic Insulator
-
Alumina Ceramic Rings
-
Pressure Sensor Ceramic
-
Advanced Technical Ceramics
-
Advanced Engineering Ceramics
-
Fuse Ceramic
-
Ceramic Connector Blocks
-
Electronic Ceramic Components
-
Magnetron Ceramic
-
Zirconia Ceramic Parts
-
Alumina Ceramic Rods
-
Mr.FarnReply very fast and easy to talk!
-
Mr.JacksonGood service and nice to talk.
ISO9001 Ceramic Protection Tube Metallized Electrical Hollow Ceramic Tubes
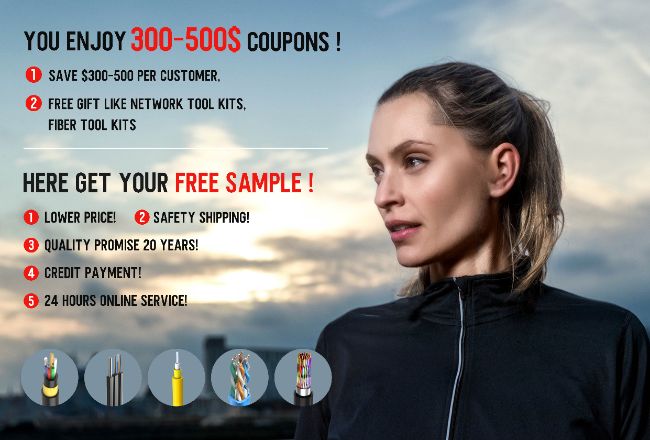
Contact me for free samples and coupons.
Whatsapp:0086 18588475571
Wechat: 0086 18588475571
Skype: sales10@aixton.com
If you have any concern, we provide 24-hour online help.
xProduct Name | Relay Ceramic Housing / Ceramic Relay Housing | Material | Alumina (Aluminum Oxide, Al2O3) |
---|---|---|---|
Insulation Resistance | 1000M Ω(1000VDC) | Thermal Shock Resistance Room Temperature To 850C | Will Not Burst Or Leak After Five Operations |
Working Temperature | -40℃-125℃ | Operate Time | ≤30ms |
Release Time | ≤10ms | Shock Resistance Functional | 196m/s² (20G Above) |
Shock Resistance Destructive | 490m/s²(50G Above) | Helium Leak Rate | < 10-9 Cc/sec |
Tensile Strength, Kovar Cup Method | > 20,000 Psi, Avg. (138N/mm2) | ||
Highlight | Metallized Ceramic Protection Tube,ISO9001 Ceramic Protection Tube,ISO9001 Hollow Ceramic Tubes |
Metallized Alumina Ceramic Tube / Metallized Electrical Ceramic Components
1. Description:
Common metalized alumina ceramics consist Molybdenum based paints followed by nickel plating. A coating of molybdenum and manganese particles mixed with glass additives and volatile carriers is applied to the ceramic surface to be brazed. The application of the coating may be hand-painted, sprayed, or robotically applied. After air drying, the coating is fired in a wet hydrogen environment at 1450°–1600°C leaving a “glassy” metallic coating 300–500 micro-inches (7.6–12.7 microns) thick, to ensure high bond strength between the metallized layer and the ceramic base.
2. Feature Advantages:
1) High elasticity modulus
2) High compressive strength.
3) Anti corrosion
4) Abrasion resistance
5) Impact resistance
6) High precision
7) High stability
8) Good advanced ceramic materials
9) High welding sealing performance
10) High hardness and high density
11) Low thermal conductivity
12) Chemical inertness
13) Good wear resistance
14) High Fracture toughness
15) Good insulation performance
3. Material Features / Properties:
Color | White or Ivory | White or Ivory | White or Ivory | |
Density | g/cm 3 | 3.82 | 3.9 | 3.92 |
Hardness | HRA | 83 | 85 | 85 |
Flexural Strength | Mpa (psi*10 3 ) | 375 | 386 | 381 |
4. Technical Parameters:
Technical Parameters of Ceramics | ||||||||
Items | Test Conditions | Unit or Symbol | 99% AL2O3 | 95% AL2O3 | 90% AL2O3 | Zirconia | Steatite | Silicon Carbide |
Volume Density | -- | g/cm3 | ≥3.70 | ≥3.62 | ≥3.40 | ≥5.90 | ≥2.60 | ≥3.08 |
Tightness | -- | Pa·m³/s | ≤1.0×10-11 | ≤1.0×10-11 | ≤1.0×10-11 | - | - | - |
Liquid Permeability | -- | -- | Pass | Pass | Pass | Pass | - | |
Flexural Strength | - | MPa | ≥300 | ≥280 | ≥230 | ≥1100 | ≥120 | ≥400 |
Elastic Modulus | - | GPa | - | ≥280 | ≥250 | ≥220 | - | 400 |
Poisson Ratio | - | - | - | 0.20~0.25 | 0.20~0.25 | - | - | - |
Thermal Shock Resistance | 800℃( Room Temperature) Cycle: 10 times | Pass | Pass | Pass | - | - | - | |
Coefficient of Linear Expansion | 20℃~100℃ | ×10-6 K-1 | - | - | - | ≤8 | - | |
20℃~500℃ | ×10-6 K-1 | 6.5~7.5 | 6.5~7.5 | 6.5~7.5 | 6.5~11.2 | - | - | |
20℃~800℃ | ×10-6 K-1 | 6.5~8.0 | 6.5~8.0 | 6.3~7.3 | - | 4 | ||
20℃~1200℃ | ×10-6 K-1 | - | 7.0~8.5 | - | - | - | - | |
Coefficient of Thermal Conductivity | 20℃ | W/(m·k) | - | - | - | - | - | 90~110 |
1000℃ | ||||||||
Dielectric Constant | 1MHz 20℃ | - | 9.0~10.5 | 9.0~10 | 9.0~10 | - | ≤7.5 | - |
1MHz 50℃ | - | - | 9.0~10 | - | - | - | - | |
10GHz 20℃ | - | 9.0~10.5 | 9.0~10 | 9.0~10 | - | - | - | |
Volume Resistivity | 100℃ | Ω·cm | ≥1.0×1013 | ≥1.0×1013 | ≥1.0×1013 | - | ≥1.0×1012 | - |
300℃ | ≥1.0×1013 | ≥1.0×1010 | ≥1.0×1013 | - | - | - | ||
500℃ | ≥1.0×109 | ≥1.0×108 | -- | - | - | - | ||
Disruptive Strength | D.C | kV/mm | ≥17 | ≥15 | ≥15 | - | ≥20 | - |
Chemical Durability | 1:9HCl | mg/c㎡ | ≤0.7 | ≤7.0 | - | - | - | - |
10%NaOH | mg/c㎡ | ≤0.1 | ≤0.2 | - | -- | - | - | |
Grain Size | - | μm | - | 3~12 | - | - | - | - |
5. Process Flows:
Formulating --- Granulating --- Forming --- Sintering --- Grinding --- Printing --- Nickel Plating --- Assembing --- Brazing --- Inspecting --- Packing
6. Production Facilities: Prilling Tower , Forming Machine , High Temperature Sintering Kiln
7. Detection Devices:
Electric Performance Tester , Film Thickness Analyzer , Granulometer , Helium Mass Spectrometer Leak Detector , Universal Pull Force Meter
8. Our advantages: Quality Assurance ; Price Competitive ; Factory Supply Directly ; Good Service
9. Shipping and Package:
Notes:Above information only for reference and please contact with us for more details freely when you have any inquiry!