-
Alumina Ceramic Components
-
Ceramic Housing
-
Metallized Alumina Ceramics
-
Custom Ceramic Parts
-
Alumina Ceramic Insulator
-
Alumina Ceramic Rings
-
Pressure Sensor Ceramic
-
Advanced Technical Ceramics
-
Advanced Engineering Ceramics
-
Fuse Ceramic
-
Ceramic Connector Blocks
-
Electronic Ceramic Components
-
Magnetron Ceramic
-
Zirconia Ceramic Parts
-
Alumina Ceramic Rods
-
Mr.FarnReply very fast and easy to talk!
-
Mr.JacksonGood service and nice to talk.
90% Electronic Ceramic Components Advanced Materials Lightweight
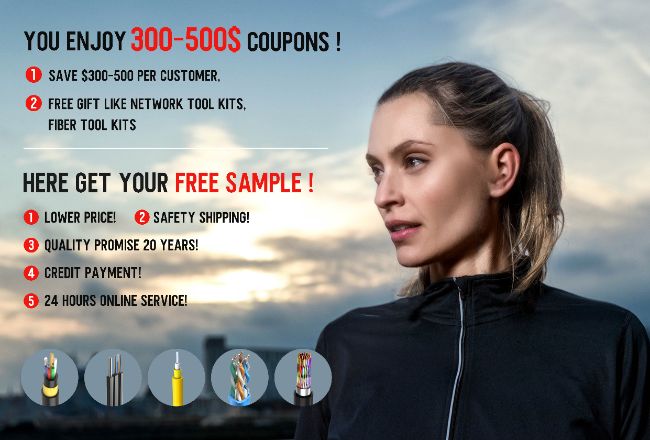
Contact me for free samples and coupons.
Whatsapp:0086 18588475571
Wechat: 0086 18588475571
Skype: sales10@aixton.com
If you have any concern, we provide 24-hour online help.
xProduct Name | Electronic Ceramic Components / Ceramic Electronic Parts | AL2O3 Content | 90% - 99% |
---|---|---|---|
Tensile | 30 Kpsi - 32 Kpsi | Flexural | 55 Kpsi - 60 Kpsi |
Compressive | 300 Kpsi - 330 Kpsi | Density | 3.7 G/cc - 3.92 G/cc |
Hardness | 13.8 HV, Gpa - 18 HV, Gpa | Thermal Conductivity | 25 W/(m K) - 32 W/(m K) |
C.O.T.E | 75 In / In°C (x10^7) - 78 In / In°C (x10^7) | Working Temperature | 1500 °C - 1750 °C |
Dielectric Constant | 9.5 - 9.8 | Volume Resistivity | >10^14 Ohm-cm |
Dielectric Strength | 16 KV/mm - 20 KV/mm | ||
Highlight | 90% Electronic Ceramic Components,Lightweight Electronic Ceramic Components,90% advanced ceramic materials |
Electronic Ceramic Components / Ceramic Electronic Parts
1. Description:
Ceramic materials are used in a wide range of applications from power distribution to smartphones.Although ceramics have traditionally been considered insulating materials, after World War II, research in material science has led to the development of new ceramic formulations that exhibit semiconducting, superconducting, piezoelectric, and magnetic properties.
Ceramic products used as electrical insulators include spark plugs, hermetic packaging, ceramic arc tubes, and protective parts (e.g., beads and tubing) for bare wires and power lines. These products are primarily used in sectors such as automotive, marine transportation, aerospace, and electricity distribution. Among these products, spark plugs represent the oldest and the most popular. They were first invented in 1860 to ignite fuel for internal combustion engines and are still being used for this purpose today. However, as the automotive industry shifts toward electric and hybrid vehicles, demand for ceramic spark plugs is expected to drop. The main suppliers of these products are directing their know-how in electroceramics toward other components such as ceramic solid-state batteries.
1) High hardness and high density
2) Low thermal conductivity
3) Chemical inertness
4) Good wear resistance
5) High Fracture toughness
6) Good insulation performance
7) High temperature resistance
8) A variety of specifications is available
9) Satisfy various technical requests
10) Lower medium spoilage
11) Stiffness texture
12) Chemical inertness
13) Good wear resistance
14) High Fracture toughness
15) Good insulation performance
3. Material Features / Properties:
Color | White or Ivory | White or Ivory | White or Ivory | |
Density | g/cm 3 | 3.82 | 3.9 | 3.92 |
Hardness | HRA | 83 | 85 | 85 |
Flexural Strength | Mpa (psi*10 3 ) | 375 | 386 | 381 |
4. Technical Parameters:
Technical Parameters of Ceramics | ||||||||
Items | Test Conditions | Unit or Symbol | 99% AL2O3 | 95% AL2O3 | 90% AL2O3 | Zirconia | Steatite | Silicon Carbide |
Volume Density | -- | g/cm3 | ≥3.70 | ≥3.62 | ≥3.40 | ≥5.90 | ≥2.60 | ≥3.08 |
Tightness | -- | Pa·m³/s | ≤1.0×10-11 | ≤1.0×10-11 | ≤1.0×10-11 | - | - | - |
Liquid Permeability | -- | -- | Pass | Pass | Pass | Pass | - | |
Flexural Strength | - | MPa | ≥300 | ≥280 | ≥230 | ≥1100 | ≥120 | ≥400 |
Elastic Modulus | - | GPa | - | ≥280 | ≥250 | ≥220 | - | 400 |
Poisson Ratio | - | - | - | 0.20~0.25 | 0.20~0.25 | - | - | - |
Thermal Shock Resistance | 800℃( Room Temperature) Cycle: 10 times | Pass | Pass | Pass | - | - | - | |
Coefficient of Linear Expansion | 20℃~100℃ | ×10-6 K-1 | - | - | - | ≤8 | - | |
20℃~500℃ | ×10-6 K-1 | 6.5~7.5 | 6.5~7.5 | 6.5~7.5 | 6.5~11.2 | - | - | |
20℃~800℃ | ×10-6 K-1 | 6.5~8.0 | 6.5~8.0 | 6.3~7.3 | - | 4 | ||
20℃~1200℃ | ×10-6 K-1 | - | 7.0~8.5 | - | - | - | - | |
Coefficient of Thermal Conductivity | 20℃ | W/(m·k) | - | - | - | - | - | 90~110 |
1000℃ | ||||||||
Dielectric Constant | 1MHz 20℃ | - | 9.0~10.5 | 9.0~10 | 9.0~10 | - | ≤7.5 | - |
1MHz 50℃ | - | - | 9.0~10 | - | - | - | - | |
10GHz 20℃ | - | 9.0~10.5 | 9.0~10 | 9.0~10 | - | - | - | |
Volume Resistivity | 100℃ | Ω·cm | ≥1.0×1013 | ≥1.0×1013 | ≥1.0×1013 | - | ≥1.0×1012 | - |
300℃ | ≥1.0×1013 | ≥1.0×1010 | ≥1.0×1013 | - | - | - | ||
500℃ | ≥1.0×109 | ≥1.0×108 | -- | - | - | - | ||
Disruptive Strength | D.C | kV/mm | ≥17 | ≥15 | ≥15 | - | ≥20 | - |
Chemical Durability | 1:9HCl | mg/c㎡ | ≤0.7 | ≤7.0 | - | - | - | - |
10%NaOH | mg/c㎡ | ≤0.1 | ≤0.2 | - | -- | - | - | |
Grain Size | - | μm | - | 3~12 | - | - | - | - |
5. Process Flows:
Formulating --- Granulating --- Forming --- Sintering --- Grinding --- Printing --- Nickel Plating --- Assembing --- Brazing --- Inspecting --- Packing
6. Application Fields:
Widely apply for new energy vehicles, charging piles, solar power generation, energy storage and power storage system, electric vehicle power system and so on.
7. Production Facilities: Prilling Tower , Forming Machine , High Temperature Sintering Kiln
8. Detection Devices:
Electric Performance Tester , Film Thickness Analyzer , Granulometer , Helium Mass Spectrometer Leak Detector , Universal Pull Force Meter
9.Order Flow Steps as belows: Inquiry ---Quotation --- Place an order --- Production --- Delivery
10. Our advantages: Quality Assurance ; Price Competitive ; Factory Supply Directly ; Good Service
11.Shipping and Package:
12. Our aimed market :
Notes:Above information only for reference and please contact with us for more details freely when you have any inquiry!